Plating
Electroplating
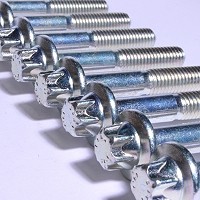
Galvanic, unalloyed zinc coating, Cr-(VI)-free passivated, additional sealant or lubricant treatment.
Chromium-VI-free
Pb-free
Cd-free
RoHS-compliant
Passivations, chromium-(VI)-free
- Blue passivation
- Transparent passivation
- Thin-layer passivation
- Thick-layer passivation
Sealants, including
- TNT 11 / TNT 15
- Delta Coll
- Finigard
- Others on request
Lubricant treatment, including
- Torque n’ Tension Fluid (TTF)
- Gleitmo
- OKS
- Others on request
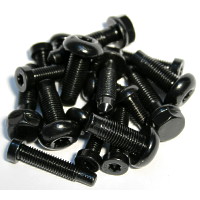
Zinc alloy coating
Zinc-iron coating, Cr-(VI)-free passivated, additional sealant or lubricant treatment
Chromium-VI-free
Pb-free
Cd-free
RoHS-compliant
Passivations, chromium-(VI)-free
- Passivations, chromium-(VI)-free
- Transparent passivated
- Black passivated
Sealants, including
- Finigard 105
- Delta Coll
- TNT
- Others on request
Lubricant treatment, including
- Torque n’ Tension Fluid (TTF)
- Gleitmo
- OKS
- TNT
- Others on request
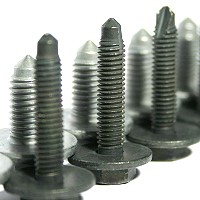
Zinc alloy coating
Zinc-nickel coating, Cr-(VI)-free passivated, additional sealant and lubricant treatment.
Chromium-VI-free
Pb-free
Cd-free
RoHS-compliant
Passivations, chromium-(VI)-free
- Transparent passivation
- Black passivated
Sealants, including
- Finigard 105
- Delta Coll
- Others on request
Lubricant treatment, including
- Torque n’ Tension Fluid (TTF)
- Gleitmo
- OKS
- TNT
- Others on request
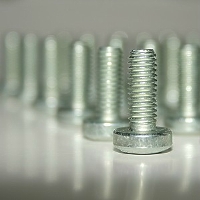
Zinklad 250
Unalloyed zinc coating, colorless Cr-(VI)-free thick-layer passivation and sealant with integrated lubricant.
Chromium-VI-free
Pb-free
Cd-free
RoHS-compliant
Layer thickness
Color
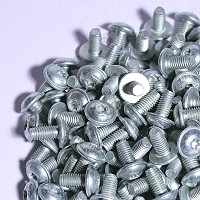
Coating for connecting elements for preventing contact corrosion with magnesium.
Zinklad MG
Unalloyed zinc coating, colorless Cr-(VI)-free thick-layer passivation and sealant
Zinklad MGL
Unalloyed zinc coating, colorless Cr-(VI)-free thick-layer passivation and sealant with integrated lubricant
Chromium-VI-free
Pb-free
Cd-free
RoHS-compliant
Layer thickness
Color
Zinc phosphating
Together with oiling, phosphating serves as a temporary protection against corrosion
- Thin-layer zinc phosphating
- Thick-layer zinc phosphating
- Oil
- Gardorol CP 8006
- Others on request
Hot-dip galvanizing
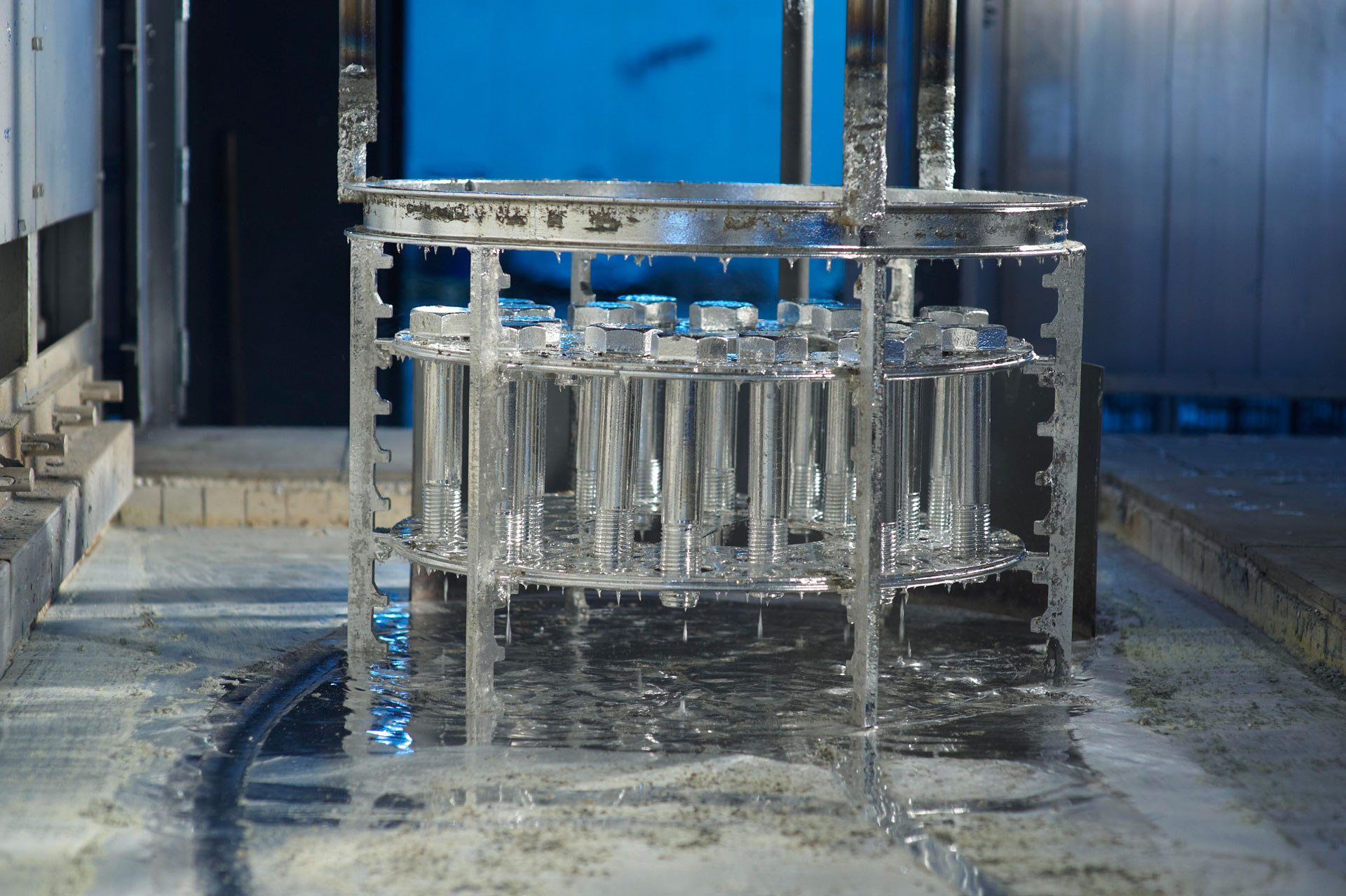
With hot-dip galvanizing, the material to be galvanized is immersed in molten zinc. As a consequence of the mutual diffusion, a layer of differently composed zinc-iron alloy layers forms between the zinc and the steel surface, whereby a coating of pure zinc usually remains on the outermost layer.
Hot-dip-galvanized parts are especially resistant against atmospheric, chemical, thermal and mechanical loads. Through the immersion in the liquid melt, cavities can also be reliably protected.
In the area of hot-dip galvanizing, we offer a unique, self-developed coating process using the rack process. The parts - such as screws for the wind power industry - that leave our system are "ready-to-build." They can be installed directly with no thread rolling - which can damage the coating.
Types of Powder Coating Materials
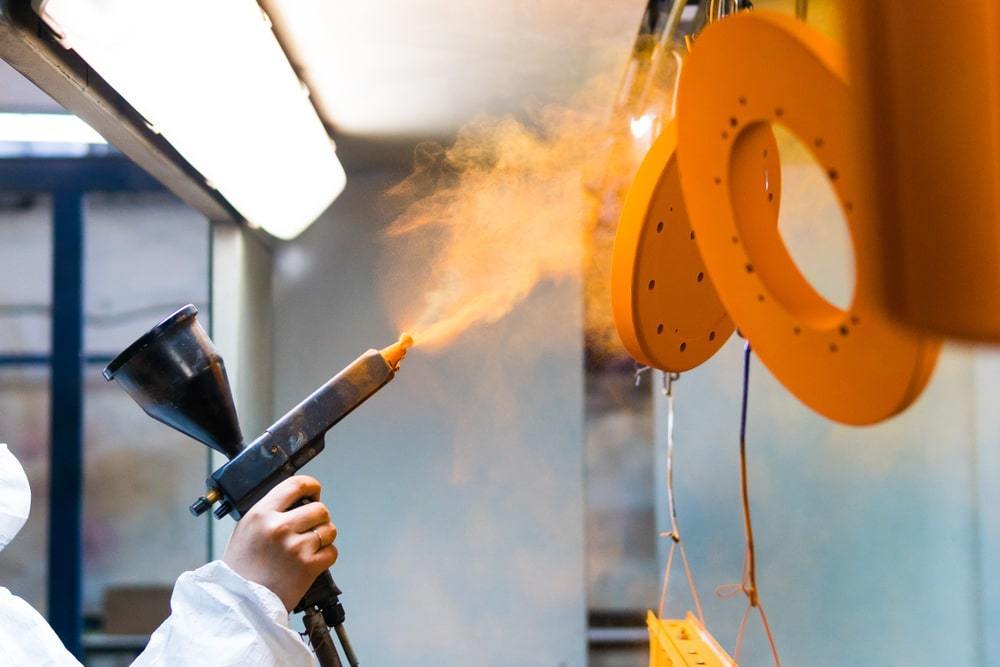
1. Thermoplastics
- Polyvinyl Chloride (PVC)
- Polyolefin
- Polyester
2. Thermosets
- Epoxy
- Epoxy-Polyester Hybrid
- Acrylic
- Silicon-Based Powders
3. New Technologies
Thermoplastics
Thermoplastics are synthetic materials that can be formed multiple times. High temperatures can melt thermoplastics, which is beneficial for reforming and recycling them but not ideal for situations where a part might be exposed to intense heat. However, several thermoplastics used as powder coats are favored for their wear- and chemical-resistance.
Nylon
Nylon powder coat is extremely durable and impact resistant. It offers excellent protection against chemicals and solvents and is FDA approved for food contact. Parts covered with nylon include food handling and dishwasher baskets. Nylon also has a very low friction coefficient, making it useful as a coating on gears and conveyor equipment.
Polyvinyl Chloride (PVC) Powder Coating
PVC coatings are pliable, sleek and durable. Like nylon coatings, they are also FDA approved for food contact, and can be used for a number of similar applications. They also are great electrical insulators for electrical lines, and work well as coatings for chain link fencing. Environmental groups, like Greenpeace, have advocated phasing out PVC because of harmful byproducts, but tests on the subject remain inconclusive.
Polyolefin
Polyolefin finishes are significantly resistant to abrasives and chemical, and offer a smooth surface and excellent adhesion properties. Due to these benefits, polyolefin coatings are used on lab equipment components that require regular cleanings.
Polyester Powder Coating
Polyester coatings weather well, look great and are resistant to abrasions. They find use in outdoor furniture, exposed automobile parts such as leaf and strut springs and are available in a diverse pallet of colors. Some polyester powders are architecturally certified for building exteriors as they shield the elements and maintain their color with only minor fading over the years.
Thermosets
Thermoset powder coating is applied the same way as thermoplastic powders. Unlike thermoplastic, thermosets go through a chemical cross-linking reaction that is non-reversible when baked. This cross-linking changes the physical properties of the plastic, typically hardening them into a solid coating. Some thermosets have the ability to withstand temperatures of over 1,000 degrees Fahrenheit and can compete with the best high-temperature enamel paints. Thermosets cure harder than thermoplastics, and as some of these thermosets harden, they also become brittle, especially in thicker coats.
Epoxy
Epoxy coated surfaces are hard and electrically insulative. They are brittle, however, and when exposed to UV light (present in sunlight) they tend to chalk and dull over time. This disadvantage keeps most epoxy-coated items indoors or buried underground as pipe coatings.
Epoxy-Polyester Hybrid
Adding polyester to an epoxy makes a softer plastic that is less likely to chip or crack. Often simply known as “hybrid” coatings, they do slightly better outdoors than straight epoxies, showing less chalking and better weathering. Their properties are similar to pure polyesters in terms of impact resistance and durability. Their applications include office furniture, fire extinguishers and toys.
Acrylic Powder Coating
Unlike epoxy-based resins, acrylics do well in sunlight and blend over a surface, leaving a high gloss, wet-looking finish that is either clear or pigmented. At present, their use as automobile clear-coat is still in development due to their brittle hardness and lack of durability. Acrylics are nonetheless used extensively on certain automotive parts, such as wheels and exposed engine parts, where the owner wants this super gloss finish.
Silicon-Based Powders
High-temperature powders are composed of silicone resins, curing catalysts and glass filler materials. These are used as exhaust system finishes in automotive and motorcycle parts and racks for ovens and barbecues. As they are able to withstand temperatures of over 1,000 degrees Fahrenheit, they can compete with the best high-temperature enamel paints.
New Technologies
One of the downsides in powder coating is its inability to coat plastic pieces due to the high heat necessary for the curing process. Traditional operations use either a standard infrared or convection oven, and temperatures are generally are close to 400 degrees Fahrenheit with cure times of 10 to 30 minutes. These temperatures and times will distort and melt small plastic parts.
Developments are underway to create new resins and powders that use ultraviolet (UV) light for curing. UV curing can be accomplished at temperatures under 200 degrees Fahrenheit in under two minutes. This allows for not only coating plastic parts, but also many other materials that cannot withstand the higher curing temperatures like various wood composites, leathers, and pre-assembled units with heat-sensitive components.
UV curable powders available now are usable in traditional Corona or Tribo guns, and come in different colors and textures. Prices for these powders can still be high, but they enable coating on products previously unresponsive to the procedure. As this technology is new, there are still potential problems associated with it. Yellow-colored powders can be difficult to coat and cure at lower temperatures and highly complex three-dimensional parts are also problematic.